Transient Process Simulation of Heat Transfer in Laser Beam Welding with an Equivalent Heat Source
The Finite Element Method (FEM) has become an established numerical tool used for different academic and industrial purposes. It allows the prediction of weld pool geometry, thermal cycle, final distortion and residual stress field during and after fusion welding. The capability of the method to predict the heat distribution in the workpiece is often used for better understanding of the process and the setting of the relevant process parameters. Mostly the calculated temperature field is experimentally validated and used as a thermal load for subsequent calculations of the corresponding (thermally induced) stresses and distortions. This kind of welding simulation is known in the literature as the thermo-mechanical model. The aim of this investigation is to provide an accurate and easy to calibrate heat source, which considers local convection effects, for heat transfer simulations of the laser beam welding process.
The numerical model is separated into two studies. The first one is the three-dimensional stationary process simulation of full-penetration keyhole laser beam welding of 15 mm low-alloyed steels thick plate in PA position at a welding speed of 2 m/min and laser power of 18 kW. The model considers the heat transfer and the fluid dynamics including phase transition, Marangoni convection and natural convection [1]. Making use of the Non-Isothermal Flow physics interface the solution of the temperature and velocity distributions in the weld pool were obtained. The second study calculates the transient thermal cycle during the laser process and the cooling stage of the part. It uses the calculated weld pool geometry from the first study as an equivalent heat source. The heat source was implemented by a Dirichlet condition using a pointwise constraint to prescribe the node temperature with the required values from the first study. The movement of the heat source was calculated using the interfaces of Deformed Geometry, Coefficient Form Edge PDE and Coefficient Form Boundary PDE.
In the investigation a framework defining the coupling of the two main models in welding simulations, in particular the above mentioned thermo-mechanical models with the process simulation was built. The link between these two models is given by the temperature history of the workpiece [2]. The simulations show that the steady state approach for the calculation of the weld pool geometry can be effectively used as an equivalent heat source in a subsequent transient study of the heat transfer. The simulated weld cross section and transient temperature field are in good agreement with experimental thermocouple measurements. It was shown, that the dynamics of the melt is an important factor for the resulting local temperature field, which defines the thermal history of the part. Consequently, an impact on subsequent mechanical calculations is expected especially when evaluating welding defects like hot cracking which depend not only on thermal cycle but also on the flow behavior of the solidifying melt.
References
[1] BACHMANN, Marcel, et al. Multiphysics Process Simulation of the Electromagnetic-Supported Laser Beam Welding. 2011.
[2] RADAJ, Dieter. Schweissprozesssimulation: Grundlagen und Anwendungen. Dt. Verlag für Schweißtechnik, DVS-Verlag, 2-5,1999.
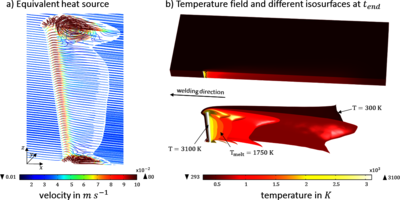
Herunterladen
- artinov_presentation.pdf - 1.78MB
- artinov_paper.pdf - 0.93MB
- artinov_abstract.pdf - 0.2MB