Thermo-Fluid Dynamics FEM Simulation of Advanced Water Cold Plates for Power Electronics
Introduction: Power electronic converters such as those for High Energy Physics Experiments (HEPEs) must operate in thermally hostile environment. Heat generated by electronics components must be conveniently dissipated to ensure electrical performances and improve reliability. Due to the high power density, the presence of closed environments, and the requirement of non-thermal interaction with other subsystems, a liquid cooling systems is mandatory. 3D FEM thermal simulations can be used for designing an optimized water cold plate for the specific application. The aim of this work is to develop a thermal-fluid dynamic FE model, accurate enough to be used in cold plate design. Setup and validation of the model: The detailed flow field and heat transfer characteristic inside the cold plate are investigated by Computational Fluid Dynamics (CFD) method, which combines the governing equations for the fluid flow with the heat convection in fluid and the heat transfer in solid equations. The relative small inlet flow rate of the studied case (around 1 l/min) suggests water laminar flow. This preliminary hypothesis was made using Reynolds number and has been confirmed by the simulation results. In order to verify the simulation results, experiments on a known cold plate have been carried out, to characterize the thermal performance at various liquid flow rates. The test bench consists of three power resistors heating the cold plate, a Teflon-Polystyrene box to maximize heat transfer towards the liquid cooling device and the instrumentation to measure the entering flow rate, and the temperature behavior of the cold plate (Figure 1). The measured parameters include, besides electrical quantities, inlet and outlet cooling water temperatures, and the cold plate surface thermal map, obtained by two dedicated thermocouples and an infrared camera, respectively. In addition, three thermocouples are integrated in the thermal insulation box to monitor the resistor temperatures and prevent overheating. Steady-state measurements (Figure 2) have been compared to simulation results in order to improve the fit and obtain an accurate model of the real device behavior (Figure 3 and Figure 4). Exploitation of the model for optimized cold plate design and thermal simulation of the whole system. The validate FEM has been used to compare several design hypothesis characterized by different path for the fluid inside the cold plate. An optimized cold plate has been designed for the specific electronic converter under examination (it will be shown in the full paper). After that, with the implemented model we have simulated the thermal behavior of the entire system composed by electronic devices mounted on the liquid heat exchanger. The comparison between simulation with actual and proposed cold plate shows the improvements that we can obtain using the solution explained in the above paragraph (it will be shown in the full paper).
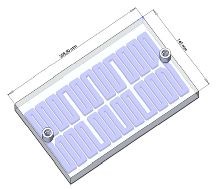
Herunterladen
- delmonte_presentation.pdf - 1.23MB
- delmonte_paper.pdf - 4.97MB
- delmonte_abstract.pdf - 0.75MB