Quantifying the Convective Heat Transfer Coefficient in a Reflow Oven: A Numerical Approach
Reflow soldering is a widely used technique in electronics manufacturing that facilitates the precise and automated assembly of electronic components onto printed circuit boards (PCBs). This method is indispensable for the efficient production of intricate electronic devices, ensuring their reliability and functionality [1]. In this work, a numerical investigation is performed in order to study the reflow process of an electronic component using COMSOL Multiphysics. Through finite element analysis, heat transfer phenomena such as conduction and convection [1] are simulated to predict the temperature distribution on the surface and in the middle of the component. To reach this goal, the surface heat transfer coefficient trend during convective reflow oven processes is determined using the Lumped Heat Capacity formulation [2]. In order to determine the trend of the heat transfer coefficient during the reflow process, a cube of aluminum (ρ = 2700 kg/m3, k = 237 W/(m⋅K), cp= 897 J/(kg⋅K)) is used (volume: 0.3 m3, see Figure 1a). . Two K-type thermocouples are used to measure the temperature trend of the element and of the air during the whole reflow process. A numerical simulation is performed by applying on the surface of the metallic block a convective heat flux characterized by the value of h(t) previously determined. Figure 1b shows the temperature trend recorded by the thermocouple inside the aluminum block (green curve), the numerical temperature inside the aluminum block (black line), and the temperature of the air inside the reflow oven (red line). The results show how the numerical findings fit well with the experimental data (see Figure 1b), with a maximum relative error of 4.3%.
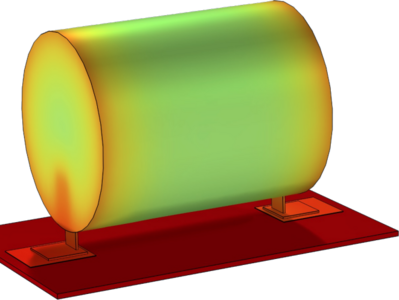
Herunterladen
- martino_9531_poster.pdf - 0.98MB