Numerical Simulations and Experimental Verification of Laser Welding of Nylon 6
Laser welding is often considered to be a superior technique over different conventional welding methods and has been gradually evolved as an efficient manufacturing process. It is a high energy density fabrication process and generally employed for fabricating intricate shapes/contours in polymers with the better precision. Nylon6 is a semi-crystalline polymer and is manufactured artificially. Due to its high durability, strength and temperature resistant properties, Nylon6 is often used as an engineering thermoplastic. In the past, joining of metals and polymers was carried out by keeping the laser beam fixed at a point, and temperature distribution along the different axes was the main concerned area of analysis, whereas a limited attention was given to residual stress analysis. Therefore, in this work, a three-dimensional (3D) time-dependent model is implemented using a finite element approach, and the process of welding is simulated in COMSOL Multiphysics. Unreinforced Nylon6 specimens are fabricated using a moving laser beam (Gaussian heat source) for a lap-joint geometry. The results of the numerical analysis are validated through experimental data. Moreover, thermo-mechanical analysis is carried out through varying the physical properties, viz., density, thermal conductivity, specific heat, Young’s modulus, coefficient of thermal expansion and Poisson’s ratio over a range of temperature to ensure accuracy in numerical analysis. Heat transfers in solid and thermal stress are the two modules that are used for the analysis of weld-bead geometry and residual stress. Fig.1 displays the meshing used during the finite element analysis of this problem. The temperature distributions obtained at the interface of the two sheets using Finite Element analysis are shown in Fig.2. The weld seam dimensions, viz., penetration depth and weld width are seen to increase with an increase in the beam radius. The amount of residual stress is mainly affected by scanning velocity.
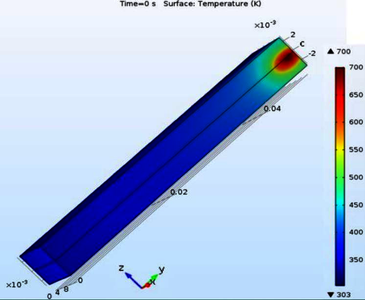
Herunterladen
- gupta_presentation.pdf - 0.6MB
- gupta_paper.pdf - 0.89MB
- gupta_abstract.pdf - 0.04MB