Numerical Simulation of Residence Time Distributions of Coiled Tubular Reactors
The fabrication of new reactor types has been simplified significantly by the rapid progression within the field of additive manufacturing. A reactor can be fit to nearly every specific task by varying its geometry and therefore its reactant hold-up and flow conditions in continuous operation. Despite the accessible freedom in the reactor design, all prototypes need to be tested with respect to their residence time distributions (RTDs). This is indispensable since the reactants should have a defined residence time in the reactor to obtain a specified product and to reduce the costs of operation. On the other hand, the testing of all prototypes will result in a high amount of spent money, time and effort.
One approach is to simulate the RTDs of the reactors with CFD before the actual printing. This allows further optimizations of the reactor before it is finally printed. As part of this work, a validated method is presented with which the RTDs of coiled tubular reactors can be simulated using the software COMSOL Multiphysics®.
The geometry of the reactor was generated using the software Inventor®. The CAD Import Module from COMSOL Multiphysics® is used to load the geometry into the user interface. The stationary flow and pressure field inside of the reactor are calculated using the Laminar Flow interface, as the inlet velocities have Reynolds numbers below 800. After the computation of the flow field, a transient species transport is simulated using the Transport of Diluted Species interface to obtain the distribution of a tracer flow inside the reactor. The molar flux at the outlet is used as a signal for evaluation.
The simulated RTDs could be matched to the experimentally obtained data as well as the mean residence time (MRT). The simulated MRTs deviate with a relative deviation of five percent for mass flow rates of 0.75 to 1.0 g.s-1 from to the experiments. Yet, adsorption effects were causing a higher MRT when being compared to an ideal system. An optimization of the reactor was carried out by imprinting static mixer elements into the fluid domain where first simulations showed a reduction of the adsorption magnitude.
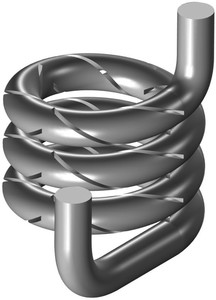