Numerical Investigation of Electrolyte Flow in a Multi-Cathode System for Electrochemical Machining
Manufacturing and finishing of components with complex internal features is a significant challenge. Industrial sectors like automotive industry, aeronautics or medical technology require these internal features with highest precision and repeatability. Such components are often machined in temporarily and locally separated manufacturing processes. Due to these separate processes, form deviations and positioning errors increase, leading to more narrow tolerances for each manufacturing process. The technology that is aimed within the project SwitchECM is supposed to enable machining of components with different complex internal features in one single production stage and simultaneously enable highest precision. Main basis of the aimed technology is electrochemical machining (ECM). Within the project a multi-cathode system will be developed, in which every single cathode can be controlled with specific parameters. Essential switching parameters are adjusted according to requirements of the predefined features. In this study COMSOL Multiphysics ® is used for numerical investigation of the electrolyte flow in the developed multi-cathode system, which is shown in Figure 1. Figure 1 shows the 3D geometry of the fluid domain. Due to the complex geometrical shape the fluid domain is split at the plane of symmetry. This reduces the number of mesh elements and the time for solving. It can be seen that the geometry of the annular gap is very narrow and is interrupted in its form by three additional geometric features. These internal features represent the machining areas. The electrolyte flow is a main parameter for the process design and the prediction of the machining results. For example, the dissipation of removed material and process gases are necessary for process stability and manufacturing quality with highest precision. By variation of the volume flow at the inlet of the multi-cathode system, it is possible to analyze the pressure drop as well as the fluid velocity and to detect areas with unwanted fluid circulation. Due to the narrow gap and the variation of the volume flow at the inlet the turbulence module k-ω is selected. The simulation shows, that a circulation of the electrolyte in the aimed machining geometries can occur. This circulation can increase the accumulation of ablated products, process gases and therefore can cause machining challenges. The generated knowledge of the fluid flow is a main basis for further design of the strategy for the electrolyte management.
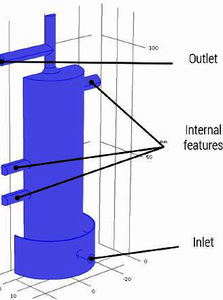
Herunterladen
- schaarschmidt_poster.pdf - 1.12MB
- schaarschmidt_paper.pdf - 0.8MB
- schaarschmidt_abstract.pdf - 0.17MB