Modeling Fluid-Structure Interaction in a Pressure-Controlled Current-Limiting Valve
This assignment deals with the modeling of a pressure controlled current-limiting valve. For this purpose the CAE-Software COMSOL Multiphysics® is used. Current-limiting valves are used as a measure of safety in many hydraulic applications. They are deployed in cases of a high decrease in pressure due to a burst pipe or leaks. The chief aim of this project is to find a beneficial modeling approach for the closing operation in order to get a detailed view of the mass-flow rate. For the seat and the body of the closing valve steel has been chosen for the material specification. For the fluid, a high viscous oil is used to achieve an operating point with laminar and isothermal flow at 20°C. The interaction between the fluid and solid domains is modelled using the FSI interface provided by the CFD Module of COMSOL Multiphysics®. Regarding the convergence, a structured mesh is beneficial. To avoid inverted cells during the closing process, the nodes are coupled to the valves displacement by using point probes. However, a complete closure cannot be achieved due to the mesh deformation, which would lead to a singularity. To minimize the mass flow through the closing gap, the viscosity is increased as a function of the clearance. The results of the transient solution are compared with steady state solutions of different back pressures using the parametric sweep study function.
Keywords: Current-limiting valve, fluid-structure interaction (FSI), plate valve, burst pipe protection, gap modeling.
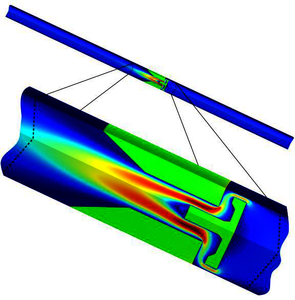
Herunterladen
- mügge_poster.pdf - 0.93MB
- mügge_paper.pdf - 1.07MB
- mügge_abstract.pdf - 0.04MB