Material Selection and Computational Analysis on DOHC V16 Engine’s Mounting Bracket Using COMSOL Multiphysics
Reduction of the engine vibration and the dynamic forces transmitting from engine to the automotive body structure has always been an important part of automotive research. Automobile engineers face the task of creating a mechanism to absorb these vibrations and provide a smooth ride. The usage of Motor Mounts is the best solution for dampening the effects of vibrations and oscillations. This paper deals with the finite element analysis and material selection and analysis for the engine accessory components. This main objective of the analysis is to minimize the weight of the mount bracket. This paper also deals with overall weight reduction of vehicle’s engine mounting bracket using different types of materials. The main parameter considered for variation in the behavior of the bracket is material variations. For different materials, the stresses are computed and compared to arrive for the best model under prescribed conditions. In the process of simulation, first the CAD model is created using CATIA V16 tool. The model will be imported to COMSOL Multiphysics for performing F.E.A. analysis on the model for suitable loading conditions and constraints. The results obtained are used for evaluation of best suitable material for the engine’s mounting bracket using the D.F.M.A. methodology.
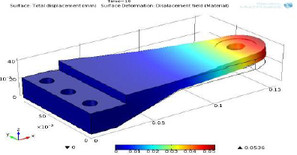
Herunterladen
- nag_poster.pdf - 0.3MB
- nag_paper.pdf - 0.28MB
- nag_abstract.pdf - 0.02MB