Interaction of Microparticles in a Miniaturized Vacuum-Cleaner
The ever-growing complexity of samples which need to be processed in e.g., environmental and biomedical/biochemical research, demand higher efficiencies of analytical techniques. Liquid chromatography (LC), mass spectrometry, among others, are analytical techniques that revolutionized the way in which chemical composition of samples of e.g., the environment, food, our body, etc. are measured. The miniaturization of LC columns has led to the use of chip columns. Up till now the efficiency of LC has been improved by reducing the size of monodisperse spherical particles, which are randomly packed in high pressure columns, and simultaneously increasing the operating pressure. To achieve a more groundbreaking progress, a paradigm shift from randomly packed beds of microparticles to perfectly ordered microparticles, is needed. This can be made possible by the latest advances in nano-meter precision positioning and material micromachining technology. The chromatographically most optimal ordered arrangement of these microparticles is proposed by using a layer-by-layer manufacturing strategy. Each layer of particles is collected using a vacuum-driven, micro-structured collection and deposition tray, and arranged with an array of precisely positioned suction holes capable of reversibly holding the particles. In our current study we model 10 micron sized particles.
The microparticles travel from a bottom plate before sticking to the suction holes at the top of the system. The velocity of the airflow in the system is an important parameter which determines if the particles will detach from the bottom surface and it also determines the particle’s trajectory. To this end some preliminary simulations have been performed with the COMSOL Multiphysics® using its laminar flow and particle tracing interface. However, the particle tracing module assumes that particles are point masses, i.e. their shape and volume are not taken into account. This is considered to be a shortcoming, since the particles in our system influence the flow field around them and inherently the flow field for neighboring particles. To this end we will study a 2D system with two solid circular objects positioned in a rectangular channel as depicted in the attached figure. We will use the laminar flow interface of the COMSOL Multiphysics® to study the influence of the following parameters on the force exerted on these two solid objects due to the flow around them: the distance d of the second circular object to the right boundary of the system, the inlet velocity and the angle α between the two centers of the circular objects. This will enhance our knowledge on the influence of particles on one another. Currently we are studying the movement of these particles using the laminar flow and fluid structure interaction interface of the COMSOL Multiphysics®
We expect that as the distance d decreases, the right boundary will exert a greater force on the second object, i.e. it pushes the object away from the right boundary. The fluid structure interaction should give us more insight what will happen with both particles hereafter. Ultimately this study will enable us to create a monolayer of particles.
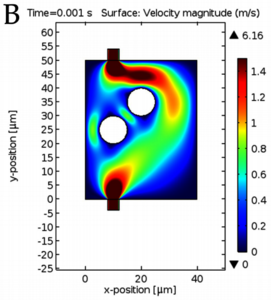
Herunterladen
- jimidar_poster.pdf - 0.77MB
- jimidar_abstract.pdf - 0.25MB