Heat Transfer Simulation for Reliability Estimation of Additive Manufacturing Process using the COMSOL Multiphysics® Software
Selective laser melting (SLM) is a popular additive manufacturing (AM) process that creates 3D metal parts by fusing fine metallic powder together. However, it remains difficult to certify AM part as its final quality can largely vary, depending on material and process variations. These variations govern its final density, residual stress distribution and microstructure, resulting in uncertainty in mechanical performance. Current practices, which often place more emphasis on post hoc qualitative approaches, are not able to quantify the mechanical performance uncertainty due to multiple input variations. Therefore, a quantitative computational approach for uncertainty analysis is used here to deal with multiple input variations and provide higher confidence in the mechanical performance of AM parts. Specifically, we developed an integrated simulation approach with COMSOL Multiphysics® software to assess the impact of input variations on the temperature distribution and history of Ti64 SLM process.
Heat transfer analysis of a single layer multi-track SLM AM process was performed with COMSOL software to calculate the temperature distribution and history, which will be used to predict microstructure evolution and mechanical properties of Ti64 in future studies. The heat transfer process was modeled by the transient heat conduction equation and the boundary conditions were characterized by heat loss via convection and radiation. The ambient temperature was kept constant throughout the simulation. The finite element (FE) mesh for the 3D thermal analysis is shown in Figure 1(a). The laser source was modeled by a heat flux with a Gaussian distribution profile. Further, we have developed a subroutine in the COMSOL add-on LiveLink™ for MATLAB® to read a laser scan path input file and create the motion of the laser source (Figure 1(b)). Mesh size study was carried out to ensure convergence of the maximum temperature (Figure 2).
The variable process input parameters considered in this study include laser power, beam width and ambient temperature. Nominal values of these input parameters were combined with an appropriate value of uncertainty (based on experience and knowledge about the process) to generate ranges for each input parameter. The parameter space was subsequently scanned using a sampling technique and the correlations between the input parameters were accounted for during sampling. The generated parameter sample sets were used for Monte Carlo simulations. Model evaluation was performed to obtain the effect of uncertainty in input parameters on output predictions. The domain temperature history was obtained using the developed COMSOL finite element model. Additionally, 95% confidence intervals were calculated for the temperature history of nine different locations in the domain (Figure 3). It can be observed that the confidence interval is wider in the region with temperature increase, corresponding to the laser beam approaching the location, and decreases once the laser beam moves away. The results can be used to establish the reliability of multi-track SLM process through parameter estimation and uncertainty analysis.
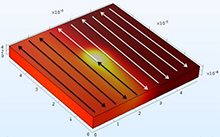
Herunterladen
- leung_presentation.pdf - 1.51MB
- leung_abstract.pdf - 0.31MB