Estimation of Tungsten Melt-Zone Size During Transient Heat Loads
Electron beam has a wide range of applications in the material processing and joining techniques. Apart from that, it has also been utilized to simulate steady as well as transient fusion reactor relevant heat loads.
Transient heat load events spontaneously occur in the fusion reactor. Several hundred megawatt of power is dumped upon the plasma facing material surfaces for a very short duration, roughly in the range of milliseconds. Tungsten is a prime plasma facing material in present as well as future fusion reactors. Cracking and melting of the superficial tungsten surface occurs during these transient heat loads [1].
The aim of this work is to estimate the size of tungsten melt-zone formed during the transient heat load event, simulated using the high power electron beam system. Heat flux distribution of the electron beam over the beam spot area is gaussian. Result obtained from COMSOL Multiphysics® software concludes that effective area of the gaussian heat pulse, where the heat flux factor is greater than or equal to the tungsten melting threshold factor ~ 20MW/m^2*t^0.5[2], is responsible for melting of the tungsten surface.
COMSOL Multiphysics® was used to estimate the size of tungsten melt-zone occurrence, due to transient heat load. Gaussian pulse was generated using COMSOL Multiphysics® with maximum heat flux 1.3E9 MW/m^2 with sigma of 3.5. Heat flux with the gaussian beam was exposed to the effective area of diameter 15 mm on the tungsten surface. Transient heat transfer analysis was carried out for time 20 milliseconds.
The simulation result shows an agreement with the experimentally observed result as well as analytically estimated radius of the melt-zone. Radius of the melted zone measured by MATLAB® image processing route is as shown in the figure, and the radius calculated using COMSOL Multiphysics® is 4.9 mm. 2D Gaussian heat flux profile considered for simulation is as shown in the figure. Figure 3-4 shows the results obtained from COMSOL Multiphysics®.
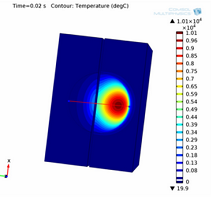
Herunterladen
- patil_presentation.pdf - 0.61MB
- patil_abstract.pdf - 0.61MB