Dynamic Simulation of a Coaxial Magnetic Gear Using Global ODE's and the Rotating Machinery, Magnetic Interface
The coaxial magnetic gear is a good alternative to classic mechanical gears. The magnetic gear has high mechanical durability, overload protection and lower noise, than a mechanical gear [1,2]. A static model of a magnetic gear [3,4] is used for simulation of the magnetic fields and mechanical forces in the steady state. For the dynamic characteristic of the magnetic gear, i.e. a run-up, slowing-down and load demand process, velocity control, is necessary to use a dynamic model of the magnetic gear. The dynamic model will be discussed in this paper. COMSOL Multiphysics® software is applied for a numerical solution of this model. The nonlinear material parameters, a small air gap size and transient dynamic simulation make this model a challenging task for realization. The two-dimensional model allows to obtain all the necessary effects except the end-effects. The coaxial magnetic gear is composed of three main parts (Fig. 1, upper): the inner rotor, the modulator, and the stator. The stator of the magnetic gear is fixed, while the rotor and modulator are rotating. The transmission ratio depends on the number of magnetic poles in the rotor, in the stator and on the number of modulator steel segments. The magnetic field is caused by permanent magnets in rotor and stator. Due to the modulator steel segments and configuration of the permanent magnets, the magnetic fields are closed between rotor and stator parts. An angular velocity is predefined on the one of two rotating parts as input of the gear. Due to the predefined external angular velocity, one part of the gear rotates and the magnetic field configuration changes. Magnetic forces cause a rotation of another rotating part of the gear. The geometrical scale in this model varies from mm in the air gap to several cm. For an accurate calculation of the electromagnetic forces it is necessary to generate an accurate mesh, especially in the air gap. This model takes into account an external dynamic load on the rotating part during rotation, for instance, the drill with a magnetic gear sticks in the material. The results will be discussed in the full paper. The calculated magnetic flux density at the time step t=0 s is depicted in Fig. 1 upper. The calculated angular velocity of the rotor in the case of the prescribed velocity on the modulator is depicted in Fig. 1 below.
REFERENCES
[1] V. Reinauer, J. Albert, R. Banucu, W. Hafla, C. Scheiblich, A. Weinläder, W.M. Rucker „Contactless torque transmission by a magnetic gear“, 17th Conference on the Computation of Electromagnetic Fields, 2009 [2] X. Liu, K.T. Chau, J.Z. Jiang, C. Yu „Design and analysis of interior-magnet outer-rotor concentric magnetic gear“, Journal of applied physics 105, 07F101 (2009) [3] W. Hafla, A. Buchau, W.M. Rucker, A. Weinläder, B. Klotz “Efficient design analysis of a novel magnetic gear on a high performance computer”, COMPEL Vol. 26 No. 3, 2007 [4] K. K. Uppalapati, J. Z. Bird, “An Iterative Magnetomechanical Deflection Model for a Magnetic Gear”, IEEE Transactions on Magnetics, vol. 50. No. 2, February 2014.
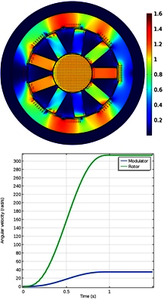
Herunterladen
- ostroushko_presentation.pdf - 0.71MB
- ostroushko_paper.pdf - 0.71MB
- ostroushko_abstract.pdf - 0.08MB