Development and Production of a Box for Storage and Shipping of HDIs in the Upgrade of the CMS Experiment
The Large Hadron Collider at CERN has begun operations at 7 TeV center of mass energy. CERN plans to run at this energy until the end of 2012 with the goal of providing an integrated luminosity of a few fb?¹ to the CMS and ATLAS experiments. The LHC will then shut down for 1.5 to 2 years to make the revisions necessary to run at ~14 TeV. Operation resumes in 2014. In 2017/18, there will be another long shutdown to prepare the LHC to operate at and eventually above the design luminosity of 2×1034 cm?²•s?¹. Operation will then resume with the luminosity rising gradually during this period to 2×1034 cm?²•s?¹. The two long shutdowns provide CMS an opportunity to carry out improvements to make the experiment more efficient, to repair problems that have been uncovered during early operations, and to upgrade the detector to cope with the ultimate luminosity that will be achieved during this period.[1] The proposed upgraded pixel detector has only one type of sensor module with two rows of 8 ROCs each. This will simplify considerably the sensor production, module assembly, and testing. The active area of the module is 16.2x64.8 mm². The pixel size will remain the same as before, 100 x 150 µm². For the sensors our baseline is to use the same n+-on-n technology as for the current detector. The sensor is bump-bonded to 16 ROCs which for Layers 1 and 2 for BPIX, will be thinned down to 75 µm. For the rest of the layers and the end-cap disks, the ROCs will be thinned down to about 200 µm. A high density interconnect (HDI) (Figure 1) is glued on top of the sensor with wire bond pads to connect to the corresponding pads on the ROCs. Electrical signals will be sent from/to the ROCs through the HDI and then to the downstream electronics. The TBM chip will be mounted on the HDI as well. A small clip is glued to the ends of the module to allow the assembly of the module to its support structure[2]. At INFN Catania we designed a box for storing and shipping of the HDIs. The study of the box was very difficult for two reasons: the box and its contents are to be sealed under vacuum and the material used to fabricate the box must not electrically charge up, that is it must be ESD-safe, yet should not be metal to limit weight. The development of the box has been performed with support of the COMSOL code and finite elements studies for both design and dimension optimization (Figure 2).
With COMSOL help, we optimized material: choice is gone PE1000UHMW. COMSOL Multiphysics code was very useful because thanks to its Structural Mechanics Module we have been able to obtain very accurate simulations of the pressure exerted on the box and thus optimize the design.
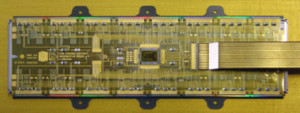
Herunterladen
- noto_poster.pdf - 1.77MB
- noto_abstract.pdf - 0.18MB