Design and Manufacturing of A Linear Induction Motor for the 2019 EPFloop Prototype in the Framework of the SpaceX Hyperloop Competition
The EPFLoop team from Ecole Polytechnique Fédérale de Lausanne has developed a capsule thanks to which it won the 3rd place in SpaceX’s Hyperloop Pod Competition in 2018. This year the EPFLoop team has been selected again to participate at the 2019 Competition held at the SpaceX facilities in Hawthorne (USA - California).
This year, the team decided to design, develop and assemble a propulsion system composed of a double-sided Linear Induction Motor (DSLIM). This kind of propulsion offers numerous advantages, removing the need for a direct contact propulsion mechanism (which provides a significant weight reduction) along with any dependence on maintaining contact between such a mechanism and the rail.
Since its performance can be analyzed and improved studying factors such as material properties or geometrical factors, in this contribution we describe the approaches that have been followed using COMSOL Multiphysics® to provide reliable results and assist in the design of the LIM.
The simulation are then compared with experimental measurements on the motor and a semi-analytic model developed by the EPFLoop team.
An optimization process has been then carried out based on simulation results. The goal was to find the best motor geometry and configuration in terms of maximum capsule speed, considering all the limitations introduced by the different subsystems, such as battery (active power limitation) and voltage source inverter (apparent power limitation).
The outcome is a complete study, design and manufacturing of the EPFLoop LIM considering magnetic saturation, spatial field harmonics, leakage flux, pole pitch, total air gap, input frequency, material resistivities and eventually studied extremity and slot effects.
The simulation results have been carried out by using the AC/DC module (Magnetic Fields and Magnetic & Electric Fields interfaces) for 2D/3D models.
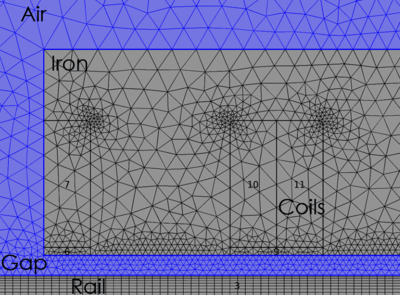