Computational Design and Optimization of Bone Tissue Engineering Scaffold Topology
Introduction: Bone tissue has a limited ability for regeneration; critically sized defects cannot self-heal and require medical intervention. Bone tissue engineering (TE) circumvents this issue by growing replacement bone tissue from the patient’s own cells inside scaffolds. TE scaffolds are porous constructs that act as a support structure during bone regeneration and helps cells attach and proliferate [1]. Ideally, scaffolds are mechanically similar to native bone, porous enough for nutrient flow, biocompatible, biodegradable, induce cellular growth, and easily fabricated. Computer simulation could improve the scaffold design process by reducing the amount of experimental tests needed [1, 2, 3]. Additionally, using the COMSOL Multiphysics® software and the COMSOL Optimization Module could aid in determining a design that maximizes compressive strength and porosity. By comparing the Optimization Module design to a commonly accepted statistical design method, we can validate simulation as a design tool in this field.
Use of COMSOL Multiphysics: To compare with physical scaffolds produced via 3D-bioplotting, a 3D model, shown in Figure 1, was generated and parameterized. Parameterization ensured that the model would be compatible with the iterative changes by the Optimization Module. The Structural Mechanics Module was used to assign linear-elastic behavior and instantaneous displacement to mimic compression tests performed on physical scaffolds. The stresses were then analyzed to determine the resultant compressive stress and modulus of the topology. Optimization methods are used to determine a design that maximizes compressive strength while maintaining acceptable porosity. The radius of the strands in the scaffold and the distance between them are used as control variables, while the porosity is constrained to >50% void space.
Results: As seen in Figure 2, the simulation can reasonably predict the Young’s modulus of the scaffold, in relation to the control variables, at low strains (10%), where the physical scaffolds behave linearly. The linear elastic assumption does not hold at higher strains, so the predictive abilities of the simulation decrease as strain is increased.
Conclusion: Results thus far are indications of the simulation’s ability to predict the experimental results in standalone tests. They do not yet account for the ability of the Optimization Module to generate a design. In order to do so, an I-optimal, split-plot designed experiment (DE), illustrated in Table 1, was developed to establish the effects of the control variables on the compressive modulus and porosity. Mechanical testing of DE scaffolds is used to generate equations relating the control variables to the scaffold’s compressive modulus and porosity. A simultaneous optimization of the equations will then suggest an ideal scaffold design. By comparing the statistical design with the COMSOL software design it is possible to determine the effectiveness of the Optimization Module as a TE design tool.
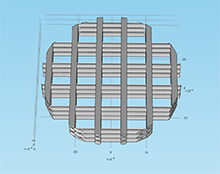
Herunterladen
- uth_abstract.pdf - 0.28MB