Analysis of 3-D Printed Structural Components for Cube Satellites
Additive manufacturing uses 3D printing to build physical parts from CAD-based designs. The technology includes fused deposition modeling (FDM) and selective laser sintering (SLS) methods. 3-D printing is of particular interest for smaller, one-of-a-kind, customizable products. A cube satellite (CubeSat) containing fiber reinforced SLS parts has been successfully launched (Ref 1).
Lower cost FDM can be less attractive for manufacturing CubeSat components, since the FDM materials cannot be fiber reinforced, and the mechanical properties are not close to aluminum. One industry solution has been to coat the 3D-printed parts. The mechanical properties can be greatly improved by electroplating a metal coating to form a sandwich composite structure. Additional benefits include EMI shielding, increased temperature capability, elimination of outgassing and reduced flammability. To properly design and analyze the component structure, the output geometry of electroplating analysis must be imported into a structural mechanics module. The research investigates performing the analysis within the framework of the COMSOL Multiphysics® software.
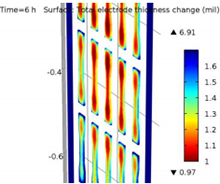
Herunterladen
- herzfeld_presentation.pdf - 0.72MB
- herzfeld_paper.pdf - 0.4MB
- herzfeld_abstract.pdf - 0.3MB