2D Simulation of Crimping Process for Electric Vehicle Battery Charge Cable
Of utmost importance in appliance design and manufacture are the features for protection from fire and for personal safety. Appliance engineers are continually in pursuit of better,longer-life appliances that will provide both lower cost to the consumer and lower energy consumption. Therefore, a 2D simulation of crimping process has been proposed using the COMSOL Multiphysics® software. Convective and conducting heat analysis results may help engineers decide the optimal crimpting shape and process.
Crimping is considered one of the most reliable metal joining technologies in the connector industry. Although it is among the oldest methods of establishing a permanent wire to terminal connection, the underlying mechanical principles of this process still become a source of heated debates within the industry’s engineering community. Even a quick literature search is guaranteed to yield a list of publications that disagree with each other and state quite opposite points of view on ‘what makes a good crimp’. The Turkish household appliances sector started production as an assembly industry in the 1950s and it has achieved tremendous growth since then. Now, the household appliances industry is one of the well-established and dynamic sectors in Turkey. The industry is mainly composed of two subsectors; namely, the white goods (durables) which dominates the sector and the small household appliances. This trade sector brings new ideas for power cables and their connector industry. Crimping process is very important in terms of power cables and connectors and undesirable problems may often occur due to its wrong usage/processes. Heat is the main problem in crimping process and should be analyzed carefully. Therefore, this paper addresses and focuses convective and conducting heat transfer study of a selected crimping process using COMSOL Multiphysics®.
The most important added value of the project is to remove the import dependency in this area by bringing domestic technology product crimp designs to white goods sector. In addition, reducing the waste and production costs of crimps product groups will directly contribute to the profitability and productivity increase in the white goods sector. In addition to this, this paper will enable new research work to be undertaken in order to examine in-depth the effects on the electrical and mechanical properties of the products' improvements in crimp designs.
Material and Methods: 242-stranded copper wire with a diameter of 0.2mm is used in crimp process. Crimp material is chosen as silver and surrounded by air in the COMSOL model. Nominal electric current of 63A is defined as rated current representing battery charge cable for electric vehicle. The model uses both electric current and convective heat transfer modules. Heat source is the total power dissipation density from electric current physics. The simulation time is set to 60min as defined in standards. Then performance curves of temperature and power dissipation are obtained. According to the simulation results highest temperature is 60C and total power dissipation is 2.04mV/mm^3.
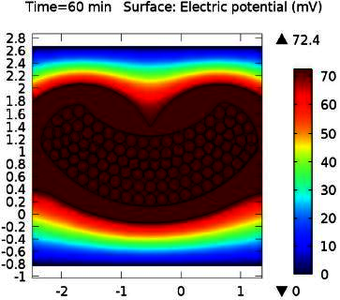
Herunterladen
- ozgonenel_poster.pdf - 0.54MB
- ozgonenel_paper.pdf - 0.96MB
- ozgonenel_abstract.pdf - 0.09MB