Modeling PCB Based Inductive Position Sensors with the COMSOL® AC/DC Module
The growing adoption of electric vehicles has led to increased exposure of cars to stray magnetic fields. To address this issue, inductive position sensors have emerged as a viable solution due to their inherent immunity to stray magnetic fields. Widespread adoption of the inductive technology is however possible only if these sensors are able to achieve the high accuracy standards (<0.5%) of the automotive industry. To ensure optimal performance, realistic simulations of the sensor's electrical behavior are necessary. Inductive position sensors are based on a set of coils implemented in a printed circuit board (PCB) and a moving metallic target. One of the coils, the transmission coil, is driven by an AC frequency in between 2 and 5 MHz, while the other coils, the receiving coils, couple to the transmission coil via the target generating target position dependent voltages form which the target position can be reconstructed. In order to accurately predict the sensor performance, simulations including the exact PCB design, as well as all the exact metallic environment around the sensor are needed. COMSOL Multiphysics® offers several simulation modules that allow achieving the above stated goal. The ECAD Import Module allows importing the PCB design files in ODB++ format, while the CAD Import Module facilitates the incorporation of eventual metallic components surrounding the sensor. The AC/DC Module allows the computation of the target eddy currents and the induced voltages in the receiving coils, while the Cluster sweep feature enables parallelization of multiple simulations. The output from the COMSOL Multiphysics® software includes three distinct voltages corresponding to each step of the target displacement. The resulting sinusoidal signals are then exported to a comma-delimited file (.csv) for post-processing using Python®. The accuracy of the inductive position sensor can be thus calculated. Various sensor configurations are compared to identify the optimal conditions that yield the highest accuracy. The results obtained from the COMSOL® simulations are validated by comparing them with real measurements conducted on the same PCB design, demonstrating a remarkable level of agreement. The ability to debug accuracy issues using simple simulations that accurately replicate the sensor's behavior during application is invaluable for efficient problem-solving. In conclusion, the use of the COMSOL Multiphysics® software provides a comprehensive platform for simulating and analyzing the performance of inductive position sensors. Through realistic simulations and validation with real measurements, the software enables the optimization of sensor accuracy and offers valuable insights for efficiently troubleshooting accuracy issues.
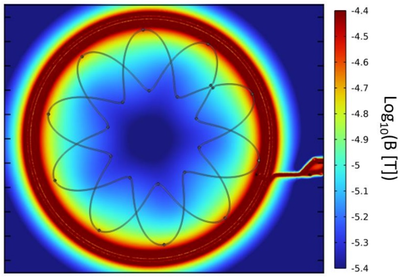
Herunterladen
- SidAhmed_5071_presentation.pdf - 1.78MB
- Comsol_paper_EID_LLG_2023.pdf - 0.78MB