Working Towards Magnetic Barkhausen Noise Detection on Curved Surfaces
Magnetic Barkhausen noise (MBN) is an emerging field in non-destructive testing, which utilizes the electromagnetic signals generated by small abrupt changes in magnetic field in a sample undergoing magnetization by an applied external magnetic field. These small abrupt changes in signal are recorded, and can help infer material properties such as surface stress, grain size and magnetic easy axis direction. MBN can be used to inspect major components, which might otherwise be costly to inspect using traditional destructive testing methods. The MBN probe induces a magnetic field in a target ferromagnetic sample, and senses the MBN as a voltage signal response in a pickup coil. The signal is generated when a complete magnetic circuit is formed between the core and sample. This work investigates the factors that affect flux coupling between the core and sample, such as an air gap. These factors help inform design considerations when attempting to measure MBN in samples with curved geometries. In this work, an analysis of a flat surface geometry is first investigated using an analytical model as well as a Finite Element Method (FEM) model. The analytical and FEM models developed for flat geometries show consistent trends, providing confidence for results obtained using both models.
The FEM model for this project was designed using the AC/DC Module in COMSOL Multiphysics® simulation software by defining two rectangular blocks as numeric coils, in the Magnetic Fields physics option, modeled as homogenized multi-turn conductors. The coils “wrap” around a rectangular core, which facilitates magnetic coupling with nearby sample, flat plate underneath the core and coil assembly. The effect of introducing an air gap (air domain) between the core/coil assembly (highly permeable steel domain) and the sample (hard steel domain) under DC conditions was the main topic of this study. A Parametric Sweep was done over different air gap values to see the related change in flux density in the core and sample. A convex geometry was simulated by making the air gap a linear function of x, related to a known radius of curvature R. The FEM results were consistent with the flat surface analytical model and what was expected from a change in air gap. FEM results were also obtained for a concave model, but refinement of the FEM model to simulate true curvature is still needed, rather than a linear approximation. Additionally, analysis must still be done to determine the effect of an AC source. Results indicate that for physical measurements the air gap between the sample and core should be reduced as much as possible. The COMSOL Multiphysics® FEM model results obtained from this work will help inform design considerations of future MBN probes for use on samples with curved geometries.
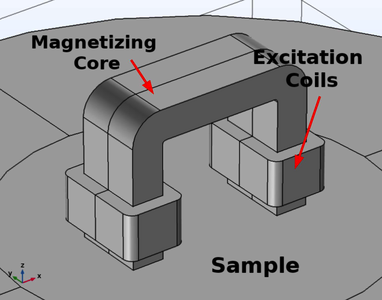
Herunterladen
- burchell_poster.pdf - 1.5MB