Stress/Strain Analysis of a Nitinol Self-Expanding Stent
Nitinol self-expanding stents are most commonly used to widen the passage of a restricted blood vessel. Unlike balloon-expandable stents, nitinol allows the stent to recover large strains caused by mechanical stresses due to its superelasticity. Self-expanding stents are first crimped to a smaller size within a delivery catheter and then placed in the correct position within the body. When the outer sheath of the catheter is retracted the stent springs back to its original shape [1]. Once placed in the patient, stents are susceptible to fatigue due to the time varying loads from the pressure variation of a cardiovascular cycle. Understanding the fatigue life of a stent is important to ensure that it functions properly during the 10 years it is typically expected to remain in patients [2]. Since experimental testing of stents can be difficult, finite element analysis is a useful tool to determine fatigue life and optimize stent designs [3].
We used COMSOL Multiphysics® simulation software to simulate a nitinol self-expanding stent in a healthy artery. We assumed that the stent and artery are rotationally symmetric and therefore modeled only 1/120 of the stent and corresponding artery wall. To generate the full model for visualization purposes we used a series of rotations, reflections, and arrays. We then applied the Lagoudas shape memory material model to the stent and modeled the artery as a hyperelastic material to account for large strains. Lastly, as we did not explicitly model the fluid flow, we applied mechanical expansion pressures to the inner walls of the stent and artery to mimic deformation due to blood flow. Figure 1 shows the deformation and Mises stress experienced in the stent at different phases of the simulation.
With the results from our simulation, we created a constant life diagram to estimate fatigue life. The diagram compares the alternating and mean strain between the simulated results and data from reference 4, which makes up the fatigue limit [4]. As our results were below the limit, this specific stent would be safe from failure at 107 loading cycles.
References
1. D. Kapoor, Nitinol for Medical Applications: A Brief Introduction to the Properties and processing of Nickel Titanium Shape Memory Alloys and their Use in Stents, Johnson Matthey Technology Review, 61, 66-76 (2017)
2. T.W. Duerig & M. Wholey, A comparison of balloon- and self-expanding stents, Minimally Invasive Therapy & Allied Technologies, 11, 173-178 (2002)
3. F. Auricchio, A. Constantinescu, M. Conti & G. Scalet, Fatigue of Metallic Stents: From Clinical Evidence to Computational Analysis, Annals of Biomedical Engineering, 44, 287-301 (2015)
4. C. Kleinstreuer, Z. Li, C.A. Basciano, S. Seelecke & M.A. Farber, Computational mechanics of Nitinol stent grafts, Journal of Biomechanics, 41, 2370-2378 (2008)
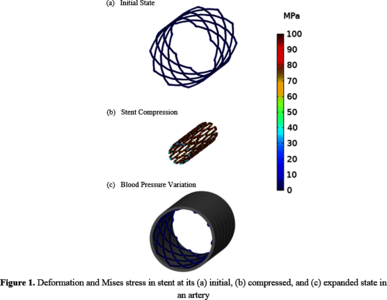
Herunterladen
- li_structural_presentation.pdf - 0.97MB