Simulation of Magnetically Driven Peristaltic Pumps for Microfluidic Applications
Microfluidic technologies can enable laboratory processes to be packaged in miniaturized and automated systems, allowing these processes to be performed with hand-held devices outside a laboratory environment. The practical usefulness of these “lab on a chip” systems has often been limited by the size, weight, or power consumption of pump and valve components, and a wider application of these systems requires the integration of small, low power pumps and valves. In this work, the performance of a small peristaltic pump is simulated using the COMSOL Multiphysics® software. The pump displaces fluid by the coordinated movement of a set of magnets that open and close adjacent sections of a fluid channel in an appropriate sequence, and the movement of these magnets is driven by another set of magnets mounted in a rotating driver assembly. The action and performance of the pump are dependent upon a variety of factors, including the number of pump magnets, the number and orientation of the driver magnets, the size and strength of the magnets, and the rotational velocity of the driver. To simulate this device, the model solves for the magnetic field, the fluid flow, and the movement of the pump magnets. The use of a sliding mesh enables the rotation of the driver, and additional moving mesh operations enable the closing and opening of the fluid channel under each pump magnet. A 2D approximation of the system has been developed to allow rapid comparison of different designs, and a full 3D model has been constructed for more accurate calculation of flow rate and maximum pressure differential.
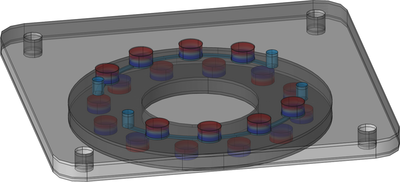
Herunterladen
- gritter_presentation.pdf - 1MB
- gritter_abstract.pdf - 0.01MB