Simulation of Laser Powder-bed Fusion Additive Manufacturing Process Using the COMSOL Multiphysics® software
Additive manufacturing technology is becoming more popular for the fabrication of metal products as it offers rapid prototyping and large design freedom. However, part quality of components fabricated by current additive manufacturing technology is not comparable to that produced by traditional methods. Lack of fusion porosity and high residual stress due to non-optimized additive manufacturing process are detrimental to fatigue properties. In order to optimize the process parameters, an efficient computational approach is needed to reduce the scope of design of experiments. In this study, we simulated the laser melting powder bed fusion additive manufacturing process using a multi-scale approach implemented with the COMSOL Multiphysics® software, Heat Transfer Module, and Structural Mechanics Module.
A micro-scale heat transfer model was developed to simulate multi-layer multi-track laser melting powder bed fusion process, estimate lack of fusion porosity due to incomplete melting, and predict the as-built density. The heat transfer simulations were calibrated with melt pool dimensions reported in literature for a range of process parameters such as laser power and laser scan speed. A macro-scale coupled thermomechanical model, based on inherent strain method, was used to estimate component-level distortion and residual stress efficiently. Two case studies were examined and comparison with experimental measurement of residual stress and distortion will be discussed. With the validated simulation models, optimization and uncertainty quantification of the laser melting powder bed fusion additive manufacturing process can be performed by conducting virtual experimental studies.
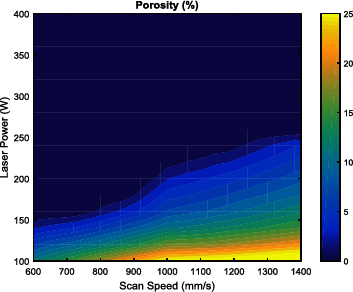
Herunterladen
- leung_presentation.pdf - 2.31MB
- leung_abstract.pdf - 0.01MB