Simulation and Verification of Bionic Heat Exchangers with COMSOL Multiphysics® Software
Bionics is the scientific discipline between biology and technology. The aim of bionics is to recognize natural design principles and derive technical solutions. Natural structures have been optimized over generations by evolution. In most cases the minimization of the energy demand is a major intend of natural optimization.
There are different designs of heat exchangers, e.g. parallel or serial channel structure, existing. But they all entail disadvantages like high pressure losses and hot spot formation. Bionic heat exchangers revert to the human blood vessel system. It is optimized for a steady and energy efficient fluid transport with low pressure losses, which are requirements for heat exchangers as well.
To analyse and verify the behaviour of a bionic heat exchanger (cp. Figure 1), a comparison between experimental test data and simulation results from COMSOL Multiphysics® software modeling was performed.
Use of COMSOL Multiphysics: Firstly a 3D CAD model of a bionic channel structure was designed. The actual heat exchanger was extruded from the channel structure afterwards. This CAD model was applied to manufacture real heat exchangers out of aluminium and for the simulation with COMSOL. The data, won from the experiments, were taken as input data for the simulations.
The thermodynamic behaviour of the bionic heat exchanger is very important, so that a time dependent study was conducted. The Non-Isothermal Flow physics interface of COMSOL was applied to generate all important results.
Results: The comparison between experimental test data and the simulation results was performed in three steps.
Pressure Loss: The average error between the real- and simulated pressure loss is 11%. On the one hand, this error can be justified with an imprecise measuring method during the experiments. On the other hand a laminar flow model was applied for simulation, but in reality there are small areas with turbulent flow as well.
Temperature behaviour: Figure
Figure 3 shows pictures, which were generated during the experiments using a thermographic camera (right side) and results from the COMSOL simulation (left side). The simulation results correspond to the experimental data with a certain, small error.
- Flow behaviour: For this comparison a special fluid was taken during the experiments. It is able to show swirls, fluid velocities and general flow characteristics in detail. COMSOL software calculates e.g. swirls of the same size and position, like the real swirl.
Conclusion: The simulation results differ, depending on the considered physical parameter, only in an acceptable extend from the experimental results. These deviations are largely attributable to inaccurate measuring methods and flow velocities in the border zone of laminar flow behaviour. On the basis of this knowledge, COMSOL Multiphysics can be verified as an extremely useful tool to design and test physical and technical processes e.g. in future work.
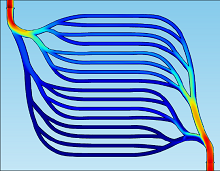
Herunterladen
- kremers_presentation.pdf - 0.98MB
- kremers_paper.pdf - 0.71MB
- kremers_abstract.pdf - 0.02MB