Reducing Loudspeaker Systems Panel Vibrations
One of the main design questions in loudspeaker enclosures concern vibrations reduction. An ideal cabinet would be infinitely rigid, so a section of an engineer work is focused on this goal.
Solutions depend by loudspeaker system audio field: Line Arrays, Automotive environments or hi-fi applications have different approaches to cabinets design, due to context and layout constraints.
Kinetic energy transmitted to panels by a loudspeaker driver is caused by acoustic radiation or mechanical transmission, particularly: •vibration from the air pressure variation in the cabinet (sound pressure inside the cabinet is generated from the rear loudspeaker membrane and it is in anti-phase compared to front membrane radiation; the sound transmitted by the panels where loudspeaker driver is fixed interferes with that from the membrane causing irregularities in both the steady-state axial frequency response curve and in the polar diagram); •vibration through the reactive force from the loudspeaker unit (loudspeaker moving assembly mass oscillations are transferred to panels through the basket by mechanical transmission); •vibration from movement of other panels (it happens widely in automotive environments).
Generally remedial treatments used to reducing resonances problems caused by baffle vibrations are bracing, damping and/or density increasing of vibrating panels. Other ingenious patented solutions are related to: •Active damping with drivers mounted in a “back to back” compound configuration (for example Bose, Kef), using also passive radiators (for example Matsushita, Bose); • Active damping with masses (for example Sony, Hikida, ASK); • Passive damping with masses (for example Genelec, Fujitsu) or decoupling air volume of the loudspeaker rear emission (for example B&W).
This study deals with a patent pending solution based on an active anti-rattle system vibrating assembly generating an inertia force, moving co-axially and in phase opposition, with the loudspeaker moving assembly. The anti-rattle system vibrating assembly uses the loudspeaker’s magnetic circuit and is constituted by a moving coil attached to a solid part and to a spring, integrated in the loudspeaker driver. The vibrating assembly study is based on the Tuned Mass Damper (TMD); starting on 2 Degree of Freedom TMD differential equation of motion, analytical solution of the ratio between mass and excursion is calculated and presented. A new loudspeaker woofer 3D virtual prototype is arranged and the project is imported on COMSOL Multiphysics® in order to study interactions between loudspeaker driver and the anti-rattle system vibrating assembly. Magnetic assembly simulations are carried out optimizing pole plates sizes and also the spring element using Von Mises stress. Then a physical woofer prototype is implemented and measured in anechoic room. Acoustical measurements on IEC panel and on a closed box with the vibrating assembly ON and OFF are compared and the real electric impedance is matched with the simulated impedance. The woofer prototype is also mounted on a baffle, loaded with a Gaussian filtered noise on its terminals and a laser scanning vibrometer system is used to measure mechanical baffle oscillations due to vibrations transmitted by the transducer. Then displacement magnitude is displayed at different frequencies with anti-rattle system ON, to evaluate panel excursion reduction.
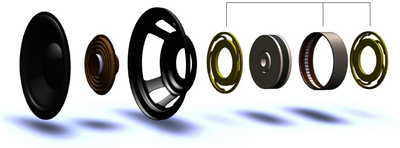
Herunterladen
- cinanni_poster.pdf - 1.2MB
- cinanni_abstract.pdf - 0.02MB