Numerical Study of the Gas-Powder Flow from Coaxial Nozzles in Laser Metal Deposition
The Laser Metal Deposition process (LMD) is a rapid free form fabrication method which can be used to manufacture new near net shape metallic components, to repair used ones or to add functional parts on existing ones. This process is composed by multiple gas streams flowing inside a complex nozzle in order to shape a powder jet which feeds a molten pool created by laser. The size, regularity and productivity of the created deposit depend on the laser powder stream interaction which needs to be better understanding and mastering. Thus, there is a clear need to figure out the gas flow and its powder stream behavior in the process to be able to control the deposit.
In this study, simulations using COMSOL Multiphysics® and based on previous works have been performed and enhanced. A two phase flow is considered, where the primary phase is the gas and the secondary phase consists of the powder particles. First, an incompressible gas is considered and its flow is solved with a CFD module using either a laminar or a turbulent model. To optimize the calculation/computation time and as the nozzle has a coaxial shape, the problem has been modeled on a 2D axisymmetric geometry. Through this model, it is possible to simulate and compare the fluid flow within the different nozzles. The aim is thus to understand any potential impact of the nozzle parameters on a built. The simulation results show a sensitive effect of the deposit tool size, outlet diameter and incoming gas flow rate on the gas outlet velocity field. The computed velocity fields were compared to experimental data obtained by measuring the pressure difference between the nozzle outlet gas flow and its environment. Most of the results have shown a good agreement, especially when one or two inlet gas streams and a turbulent model are used.
After the gas flow validation, the Particle Tracing module was used to simulated the feeding material flow. Using a realistic particle size distribution (Gaussian) and considering the particle rebound with the nozzle walls, the model can reveal the trajectory and the velocity of each particles. These two-last information lead to the jet shape estimation and its powder focal plan position.
In conclusion, COMSOL Multiphysics® software provides an efficient way to understand the gas and powder flow behavior produced by the LMD process and can reveal the effect of the nozzle geometry.
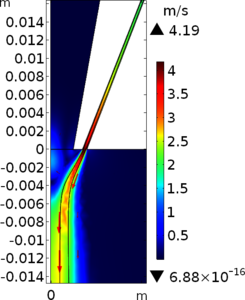
Herunterladen
- ferreira_presentation.pdf - 1.72MB
- ferreira_poster.pdf - 1.6MB
- ferreira_paper.pdf - 0.86MB
- ferreira_abstract.pdf - 0.04MB