Non-linear Solid Material Modeling in COMSOL: Utilizing Advanced Testing and Parameter Optimization
Polymers are increasingly used in many sectors, including consumer products and electronics, automotive and aerospace industries, medical devices and biopharma, and clean energy and batteries. These industries extensively use Multiphysics simulation to predict product performance, optimize design, and prevent failure during service. Advanced simulations require correctly modeling the non-linear and time-dependent response of polymers, and COMSOL Multiphysics has advanced solid mechanics constitutive models to capture these effects. Well calibrated material models based on high-quality test data must first be obtained in order to capture time-dependent non-linear effects in COMSOL Multiphysics®.
To capture the unique time-dependent constitutive response of polymeric materials, we’ll first discuss how to collect test data using advanced mechanical test methods including Digital Image Correlation (DIC), unique loading conditions, and specialized high-rate test systems. We’ll then discuss how to use the COMSOL Solid Mechanics and Nonlinear Materials modules with parameter estimation and optimization workflows to select and calibrate constitutive models based on the test data. In particular, we’ll discuss how to capture the viscoplastic response of certain polymeric materials. Figure 1 depicts the workflow of a typical material test, model and simulation workflow.
We’ll also discuss how to validate material models with additional tests involving a multiaxial load state to ensure that the selected constitutive model and parameters are accurate and robust. We’ll consider a few examples that demonstrate the power and value in utilizing accurate, rate dependent, non-linear material models. We show an example in Figure 2: a model of a small punch test that induces a state of biaxial tension and is often used in medical device fields and the nuclear industry.
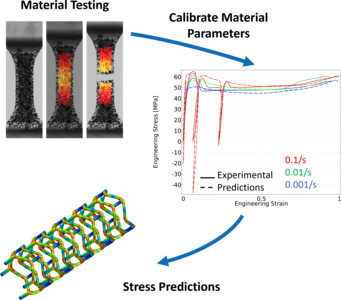