Multiphysics Modeling and Development of Automotive Heat Exchanger for Exhaust Heat Recovery
An Internal Combustion Engine (IC Engine) is a heat engine where combustion of air-fuel mixture occurs in a combustion chamber. The combustion of chemical fuels produces energies in form of heat and pressure. The pressure energy then converted to mechanical work through piston, connecting rod and crankshaft while the heat energy is exhausted to atmosphere. The Internal Combustion Engine (ICE) does not efficiently convert chemical energies to mechanical energy. A majority of this energy is dissipated to engine coolant and atmosphere as heat. Approximately 75% energy is wastage while remaining 25% used for vehicle operation which is a huge loss in terms of fuel efficiency. Rather than directly increasing fuel efficiency of the engine, exhaust heat recovery technologies are proposed to improve fuel efficiency indirectly by converting waste heat to electrical energy. Developing an optimized exhaust heat exchanger for automobiles is a challenging task in automotive industry. The advancement in multiphysics cae simulation technologies makes it possible design complex exhaust heat exchanger for efficient heat recovery, which energy can later be used to produce useful work. In this work a heat exchanger model is developed for efficient heat recovery from exhaust gas while reducing the heat energy dissipated to atmosphere. The heat transfer, cfd and design modules of COMSOL Multiphysics® software is used to develop the optimize exhaust heat exchanger for maximum heat recovery.
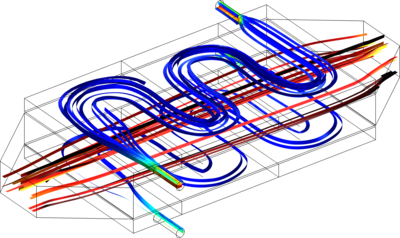
Herunterladen
- prasad_presentation.pdf - 1.15MB
- prasad_poster.pdf - 1.25MB
- prasad_paper.pdf - 1.99MB
- prasad_abstract.pdf - 0.06MB