Modeling the Hyperloop with COMSOL®: on the Design of the EPFLoop Pressurized Systems
The Hyperloop is a concept system targeting passenger transportation aiming to carry people in a pod running in a high vacuum tube at 1200 km/h. In 2015, SpaceX announced that they would sponsor a Hyperloop pod design competition, because of their interest in helping to accelerate the development of a functional Hyperloop prototype. The EPFLoop team has been formed in September 2017 at EPFL with the intention of participating at the third edition of this competition which took place in July 2018. The EPFLoop Team (http://hyperloop.epfl.ch/) groups PhD, master and bachelor students in a highly innovative environment that tackles the future of transportation. This year, over 5000 teams applied in October to participate in the competition and only 20 teams passed the final selection. EPFLoop is proud to be one of the teams in the final round.
One of the technical challenges was the design of composite subsystems such as the pressure vessels. Three pressure vessels (PVs) of different shape and structure are used to store electrical components in a pressurized environment (atmospheric pressure) in an external environment at 8/1000th of the atmospheric pressure. The PVs’ failure under load was studied using a stationary simulation of shell-like elements, representing the plies of carbon fiber-epoxy and foam. The load condition was represented by the maximum deceleration (2.6g) and the internal pressure of 1 bar. A curvilinear coordinate interface has been used to define the properties of the carbon plies on a complex geometry. The composite is locally reinforced where the deformation due to the pressure is the largest. A stationary simulation was done to design the plies layering with a minimum Tsai-Wu safety factor of 2 everywhere. Furthermore, a parametric sweep was used to find the maximum allowable working pressure (MAWP, corresponding to a safety factor equal to 2) and the BURST pressure (with a safety factor equal to 1). Principal stresses were studied, particularly at MAWP and BURST. To ensure vacuum tightness, the PVs have been experimentally tested at EPFL: to test MAWP and BURST, the PVs were loaded at 1.6 bars and leakages were checked. Encouraging and reliable results confirmed the design and analysis carried out using COMSOL. Eventually, to ensure the normal function of electronic components, the temperature inside the PVs should not go above 50 °C, due to internal electronic heat loads. Two analyses were devised. The first one has the objective of determining the maximum temperature reached in vacuum during the 40 minutes during which the pod will stay idle in the tube before the run. A heat transfer model in solids has been coupled with a laminar flow simulation to take into account the convection effects. The same model has also been studied with the maximum thermal loads during the run, in about 15 seconds. For this model, heat transfer in solid was sufficient and convection was not taken into account. The simulations were validated by measurements during experimental tests. The pressure vessels will be shown at the COMSOL Conference Lausanne 2018.
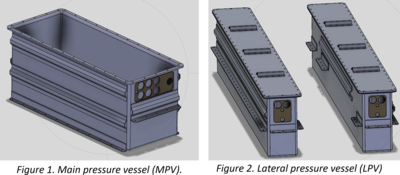
Herunterladen
- riva_poster.pdf - 1.47MB
- riva_paper.pdf - 3.81MB
- riva_abstract.pdf - 0.1MB