Evaporative Cooling in Solar Absorption Chiller
Solar cooling systems based on evaporation and absorption processes have been actively studied and different mechanisms based on various refrigerants are designed and developed. Amongst these systems, a single-stage close cycle design utilizing lithium bromide salt and water (LiBr-H2O) solution as the working fluid has been proved to be one of the most appropriate and low cost system for solar applications as it requires relatively low as well as wide ranges of operation heat source temperatures. In this design, water in the solution is vaporized by solar heated media and then condensed by cooling media in a closed chamber at reduced pressure. The separated water is then sprayed into another chamber at a much lower pressure causing the water to evaporate and thus releasing latent heat to cool media running through the chamber. The water vapor subsequently mixes with the high density salt solution resulted in the first step via absorption to return it back to initial density ready for next cycle. In this study, emphasis are placed on the modeling and simulation of the evaporation process when the water is sprayed into the second chamber as it directly affects the cooling of the media running through it. An evaporator with two aluminum foils and two tubes with cooling media running through are modeled as a representative unit of a heat exchanger in the evaporative cooling chamber shown in the figure. Using the 'Evaporative Cooling of Water' example in the application libraries as a reference, the Heat Transfer, CFD, and Chemical Reaction Engineering modules in the COMSOL Multiphysics® software are used to model the heat transfer, water vapor flow, and evaporation of the water in this process respectively. The heat transfer includes the latent heat released during evaporation of a thin layer of water on the surface of the evaporator, and the conduction between the evaporator and the cooling media in the tubes. As the water continuous to evaporate, water vapor pressure increases causing it to flow into the lower pressure absorber in which the water vapor is condensed. This pressure difference results in continuous flow of water vapor from the evaporator to the absorber that is modeled using the low Reynolds k-ɛ turbulent flow model in the CFD module. The Chemical Reaction Engineering module is used in the low pressure air domain surrounding the evaporator to obtain correct amount of water evaporating from the evaporator surface since it depends on the relative humidity of the air domain. This work studies how do system parameters including pressure, humidity, and flow of the water vapor affect the cooling of the media running through the tubes. The ultimate goal is to be able to optimize these parameters for higher efficiency.
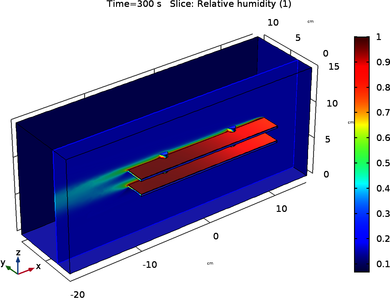
Herunterladen
- ma_presentation.pdf - 0.92MB
- ma_paper.pdf - 0.89MB
- ma_abstract.pdf - 0.06MB