Design and Simulation of Piezoelectric Micropump and Microvalve based Drug Delivery System
In the emerging field of MEMS microfluidics, micropumps and microvalves are two of the most important devices with a wide spectrum of applications such as programmable drug delivery systems, lab-on-a chip devices, µTAS (micro total analysis system), micro electric cooling applications etc. These microfluidic components are dominating the MEMS applications by virtue of their improved performance and reliability, cost and surface area reduction, etc. Micropumps convert the applied electrical energy into kinetic energy of the fluid, while microvalves maintain the directionality of fluid flow in a microfluidic channel. The aim of this work is to develop micropumps, microchannels and microvalves and combine them to develop a complete system that can be used in any of the said application fields with appropriate modifications. The micropump is modeled and simulated using COMSOL Multiphysics using solid stress-strain, piezoelectric and incompressible Navier-Stokes modes. In order to simulate the microvalve, the following physics interfaces in COMSOL Multiphysics were used: Incompressible Navier-Stokes, plane Strain and moving mesh. Static and transient behaviour of each of the components of the micropump and the microvalve, along with the fluid model is studied. A mechanically operated micropump consisting of two pump chambers closed with flexible polymer diaphragms actuated by piezoelectric actuators is designed and simulated [Figure 1]. The periodic motion of the diaphragm causes periodic change in the fluid volume and pressure in the pump chamber. Two diffuser/ nozzle elements attached to the pump chambers act as flow rectifying elements directing the fluid flow from the inlet to the outlet. The pump chamber dimensions are 5mm × 5mm × 0.2mm, and the length of the diffuser/ nozzle elements are 18mm. With an applied sinusoidal voltage of 10V amplitude, the maximum deflection of the pump diaphragms is about 10µm [Figure 2]. The data collected during the simulation process is used to calculate the resonance frequency (169.8 Hz) and flow rate (375 µL/ min) of the pump. The delivery of drugs or other fluids to the destination using a micropump is affected by undesirable backflow of liquids. In such cases check valves that behave as microfluidic diode, becomes necessary. Like an electronic diode which prevents current ?ow in one direction under the action of reverse bias, the ?uidic diode prevents ?uid ?ow in a certain direction due to the effect of back pressure and serves the function of a recti?er. The device is based upon a mechanical effect in which a ?ap made of Poly-Di-Methyl-Siloxane (PDMS) blocks channel junction in one direction to prevent backflow of fluids and opens in the ?ow direction. The effect of various flap parameters such as flap width, height and distance of the flap from the channel junction on the displacement of the flap and the flow rate of fluid through the diode is studied. The flap movement under the action of back pressure and actuation pressure is also analyzed. Thereafter, the micropumps and the microvalves are combined with microneedles to develop a drug delivery system capable of functioning irrespective of the back pressure.
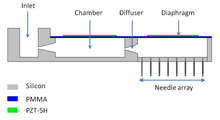
Herunterladen
- samajdar_paper.pdf - 1.33MB
- samajdar_abstract.pdf - 0.09MB