Cooling process optimization through a three-phases thermo-hydraulic model
In order to optimize the industrial “ammunition cooling” process, a COMSOL Multiphysics® model is proposed. A shell body filled with a melt-cast explosive formulation is poured and cooled by circulation of a heat transfer fluid. The solidification of the explosive composition has several thermal and fluidic consequences. To account for the solidification enthalpy, the “modified heat capacity” method is introduced to the model. Besides, the solid and liquid phases have very different densities. This results in convection within the liquid explosive composition part which requires solving the Navier-Stokes equations under their weakly compressible form. The free surface of the mixture varies thanks to a moving mesh, and the solid phase is modelled through a zero velocity in the Navier-Stokes equations. The cooling process ensures a controlled loss of heat throughout the shell, from its bottom to its top. This allows for a continuous and unique solidification front. The top of the shell is maintained above the solidification temperature whereas the bottom of the device is cooled by pulsed air or water. Thanks to the simulation results, the industrial process has been optimized by reducing the cooling time and improving quality. The app previously developed in 2017 has been improved to account for the physical phenomena which are introduced. COMSOL Server™ enables a remote computing to the users, thanks to an https secured internet connexion.
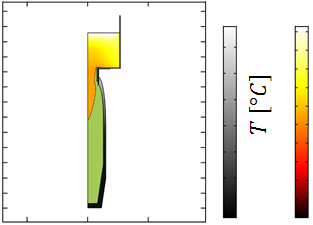