Can poroelasticity predict the response of fluid-impregnated foams to axial compression ?
Started in March 2020, the SOFITT project (Saturated Open-Cell Foams for Innovative Tribology in Turbomachinery), funded by the ANR (French National Research Agency), aims to develop reliable, high-performance, and environmentally friendly solutions for the guidance and support systems of turbomachinery through the analysis of fluid/structure interaction in porous materials. The study of this interaction has led to the implementation of a new biomimetic lubrication mechanism called: eX-Poro-HydroDynamic (XPHD) lubrication. This innovative lubrication technique is based on self-sustained fluid films generated within compressible liquid-impregnated porous layers (Ennazii, 2024).
An important aspect of the XPHD lubrication process is the mechanical response of the impregnated porous medium to the stress imposed by compression. In the case of the ANR SOFITT project, this mechanical response was studied with a study on the mechanical and morphological characterization of open-cell polyurethane foams subjected to compression. This compression study of polyurethane foams was primarily experimental, with no numerical model available to reproduce the experiment. Compression tests were conducted on dry foam and oil-impregnated foam. The obtained curves show a decrease in the plastic deformation plateau when the polyurethane foam is impregnated with oil. This decrease in the plateau in the stress-strain curve of the impregnated foam is explained by several physical mechanisms. The oil acts as an internal lubricant, reducing friction between the cell walls and facilitating their collapse at lower stresses. It also modifies the stress distribution, promoting more homogeneous deformation and introducing viscous components that dissipate some of the deformation energy. Finally, the interactions between the oil and the polyurethane alter the local elastic properties, lowering the overall stiffness of the foam and the stress required for deformation (Lacaj, 2023).
This work presents the development and validation of a numerical model using COMSOL Multiphysics to simulate the uniaxial compression of dry and oil-impregnated polyurethane foams, as part of the ANR SOFITT project. The main objective of this work is to analyze the mechanical behavior and associated flow phenomena of these porous materials. A numerical model was designed to evaluate the capability of COMSOL Multiphysics to simulate foam compression with its poroelasticity module. Simulations showed good agreement between experimental data and numerical predictions for dry foams, partially validating the model. However, discrepancies were observed for oil-impregnated samples, particularly regarding stress reduction due to oil impregnation. The pressure distribution and Darcy velocity field streamlines were analyzed to understand fluid flow through the impregnated foam. The results indicate that compression generates a pressure gradient that influences the internal fluid dynamics. This work partially validated the numerical model for dry foams and highlighted additional challenges posed by oil impregnation (Sanchez, 2024).
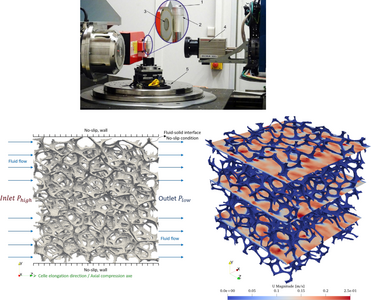
Herunterladen
- beaudoin_10181_poster.pdf - 0.51MB