Battery Cell Anomaly Detection via IAV Virtual Battery Testbench Based on COMSOL API
Automotive battery development requires continuous improvements to be more time- and cost-efficient. Limited availability of prototype cells at various stages of design or of differing chemistry, age and health is a major challenge. A highly integrated model-based developing process can enhance engineering effectiveness. This lends support to the series development or optimizes performance, against typical requirements of automotive applications beginning in early stages of development. Safety is one of the key aspects considered in the development of Electric Vehicles (EVs) and early detection of cell anomaly can serve to prevent catastrophic battery scenarios like thermal-runaway and thermal propagation. Electro-Physicochemical Models (EPCM) can provide high-fidelity simulated cell data in the absence of cell prototypes. These models can be used for benchmarking different cell chemistries, designs, or performance metrices (e.g. fast charging capabilities). They can support development and optimization of Battery Management System (BMS) functions including safety relevant topics like anomaly detection. To fully leverage EPCMs, they must be seamlessly integrated into existing development tools chains for model-based development. Our presentation focuses on coupling a set of pseudo-two-dimensional (P2D) cell models built with COMSOL® Multiphysics into a toolchain for battery cell anomaly detection implemented in SIMULINK®. Variable internal short circuit resistances are used to mimic faulty cells. The anomaly detection algorithm needs to be able to detect these, while the balancing algorithm actively counteracts the drift in state of charge (SOC). Therefore, a coupled setup of a BMS software model and cell models is required to fulfill the task. Utilizing the COMSOL® Application Builder and Compiler™, the cell models are packaged into an app and then compiled. Subsequently, COMSOL® API and Java code couple the app with the third-party software simulation environment for co-simulation. The BMS software model defines the scenario (e.g., requested current, balancing). The COMSOL® app returns the necessary signals like single cell voltages that are in turn used as inputs for different anomaly detection algorithms, which identify abnormal behavior based on the cell voltage during idle and runtime. The coupling of both balancing and anomaly detection functions is demonstrated, and the viability of different anomaly detection algorithms is successfully verified. This approach significantly enhances the usability of COMSOL® battery models for automotive system and function development within the existing toolchains. It also simplifies usage of COMSOL® models, by decoupling model generation and (compiled) model application for interdisciplinary teams with limited COMSOL® experience and license availability. This presentation is based on published work presented at the International Battery Seminar & Exhibit (Orlando, USA) in 2024 [1].
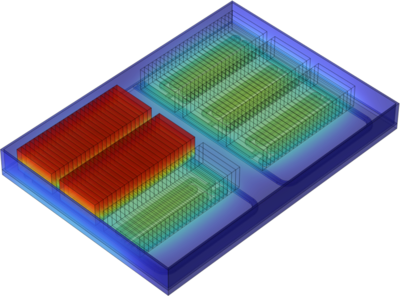
Herunterladen
- werfel_8681_poster.pdf - 0.89MB
- 1_johannes_werfel.pdf - 1.51MB