Analysis of the Stress and Load Distribution of a Bolt with Threaded Contact Modeled in 3D
A bolt connection can be modeled and simulated in different ways. In many engineering cases, only the stresses in and the contact pressure between bolted parts of an assembly are of interest. Here in this work, a bolt with thread and matching screw nut has been modeled in 3D in order to simulate the load distribution of the 3D thread contact. This is numerically challenging, because mechanical contact modeling can be a highly nonlinear problem especially with this helical contact of the threads. For this reason, numerical stabilization methods were applied. The module „Solid Mechanics“ has been applied for an assembly and the contact method chosen was "Augmented Lagrangian" as the most accurate method for determining contact pressure. The system has been meshed relatively finely to resolve the geometry with the fillets resp. root radii at the bases of the thread. In addition, the contact surfaces have been finely meshed so that the most accurate surface pressure profile possible can be simulated. This has led to the fact, that of lot of temporary memory (RAM) and PC-side calculation time has been required. Cloud computing has been used for this purpose. The goal of this work is to determine reliable results of the stress and contact pressure distribution of the described bolted joint using studies that are as accurate as possible in terms of the geometry. In for example Roloff/Matek as generally recognized technical literature, a load share of approximately one third or 33 % of the first thread of six threads engaged in total is displayed besides a shown load distribution. This is compared to the simulation results. In addition, another aim of this work was to provide simulation results in the most descriptive form possible.
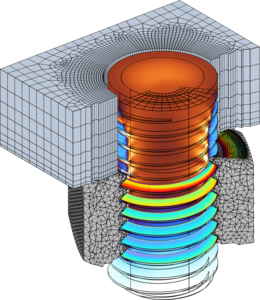